Aerospace Solutions
Deliver the standards of commercial and military aviation with parts that exceed traditional production limits.
Engine & Turbine Hardware
Print high-temperature nickel and titanium alloys for blades, vanes, and combustor components
Cabin and Structural Parts
Produce cabin brackets, fittings, and structural braces with weight-saving lattices.
Certified Quality
AS9100D-certified processes ensure traceability, uniform density, and material properties that meet aviation regulations.
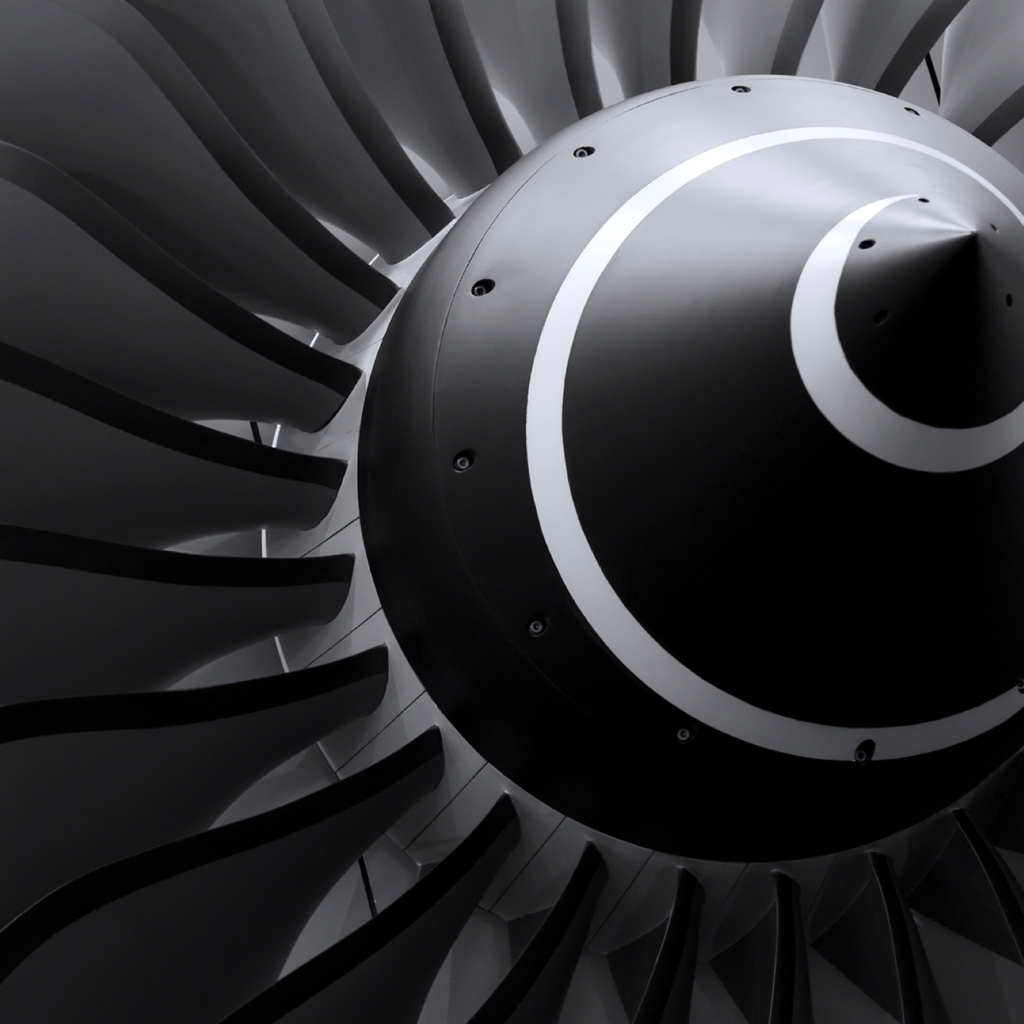
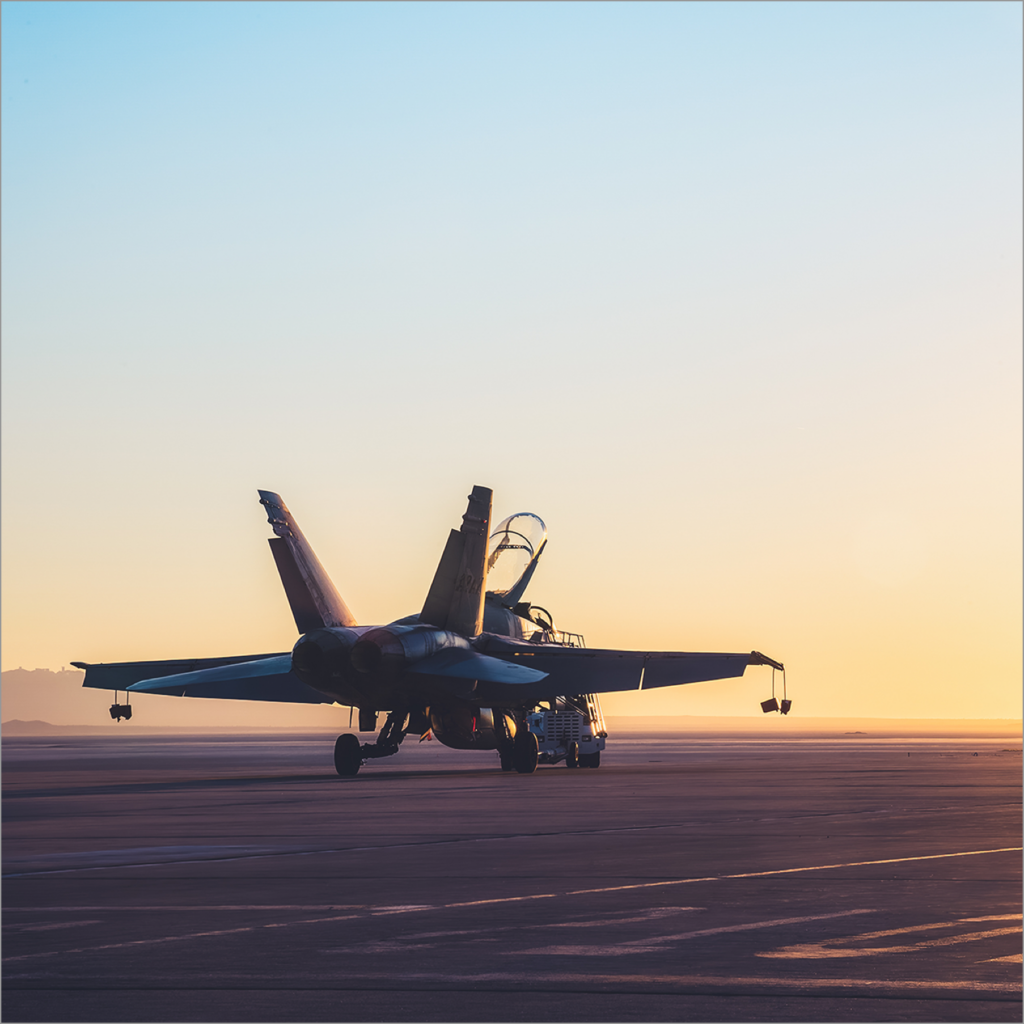
Defense Solutions
In defense applications, reliability and performance are non-negotiable. i3D Manufacturing delivers mission-critical metal components—such as launch hardware, guidance system brackets, and ruggedized enclosures—using precision DMLS® technology and rigorous quality controls.
Rapid Prototyping & Qualification
Accelerate testing cycles with complex geometries built to AS9100D standards, so you can iterate quickly and qualify parts faster.
Lightweight, High-Strength Parts
Achieve weight savings through topology optimization and hollow builds, while maintaining 99.9% density and material properties that exceed traditional forgings.
Secure, Compliant Production
ITAR-registered facilities and FFL licensing at both sites ensure full traceability and compliance for sensitive defense contracts.
Space Solutions
When every gram and micron counts, i3D Manufacturing delivers flight-ready components engineered for the harsh realities of space.
Ultra-Lightweight Structures
Leverage topology optimization to cut mass while preserving structural integrity.
High-Temperature Alloys
Print refractory metals that withstand extreme thermal cycles encountered in vacuum.
Complex, Integrated Assemblies
Combine multiple functions—like mounting fixtures and fluid channels—into single, reliable parts.
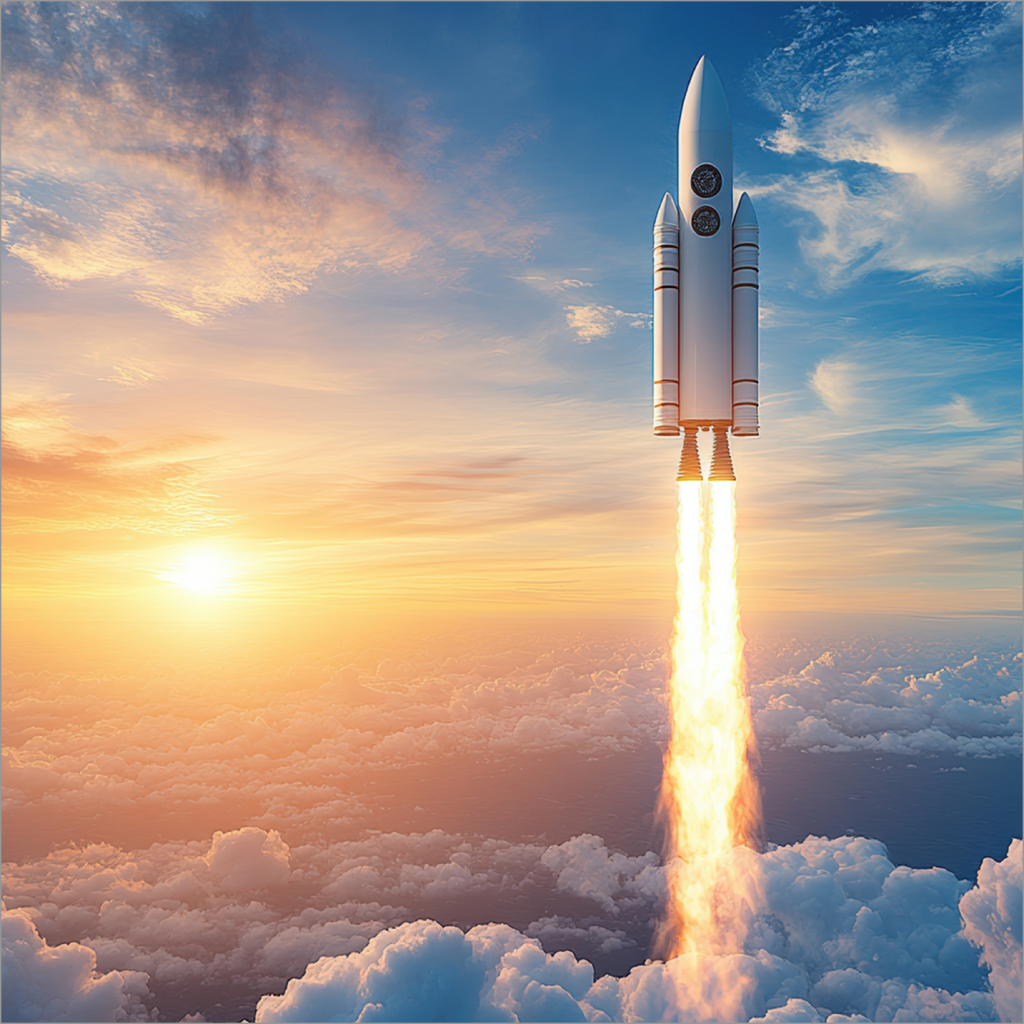
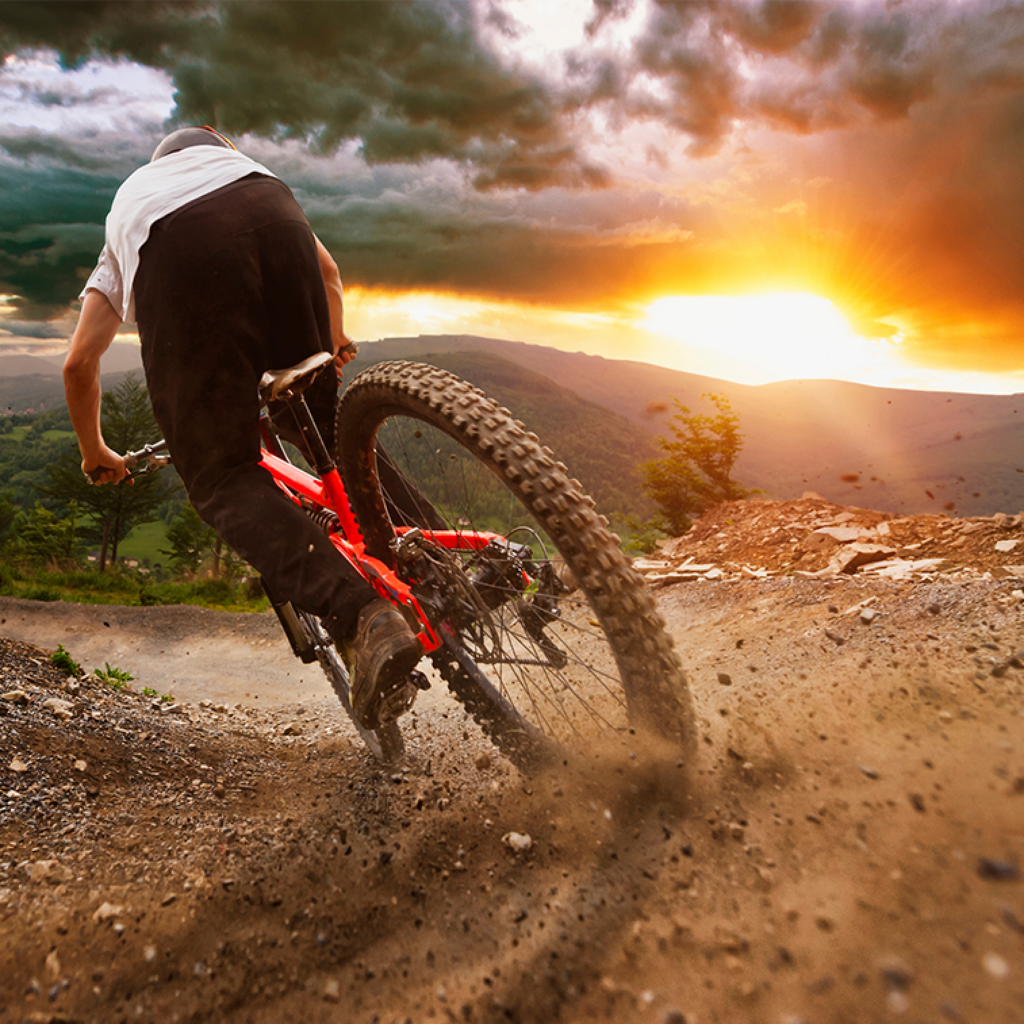
Recreation Solutions
In the world of sports and outdoor gear, weight savings, strength, and customization set winners apart.
Titanium Bicycle Parts
Reduce material waste by up to 70% versus billet machining, while enabling complex, topology-optimized frames and components that balance stiffness with lightness.
Water & Mountain Gear
Achieve up to 30% part-efficiency gains and 60% less scrap in rugged, corrosion-resistant assemblies—printing single-piece designs with integrated lattices, conformal cooling channels, and no welds or fasteners.
Titanium Golf Components
Cut traditional scrap by 50–70% with high-density DMLS® builds, producing club heads and inserts that retain machinability and deliver superior performance through intricate geometries.
Medical Solutions
When patient safety and performance are paramount, trust metal 3D printing for implants, instruments, and devices.
Bio-Compatible Materials
Utilize medical-grade titanium and stainless steels that promote osseointegration and biocompatibility.
Patient-Specific Geometry
Customize implants and surgical tools to exact anatomical data for better outcomes.
Sterilization-Ready Parts
Print parts with smooth surface finishes and no internal voids for reliable sterilization.
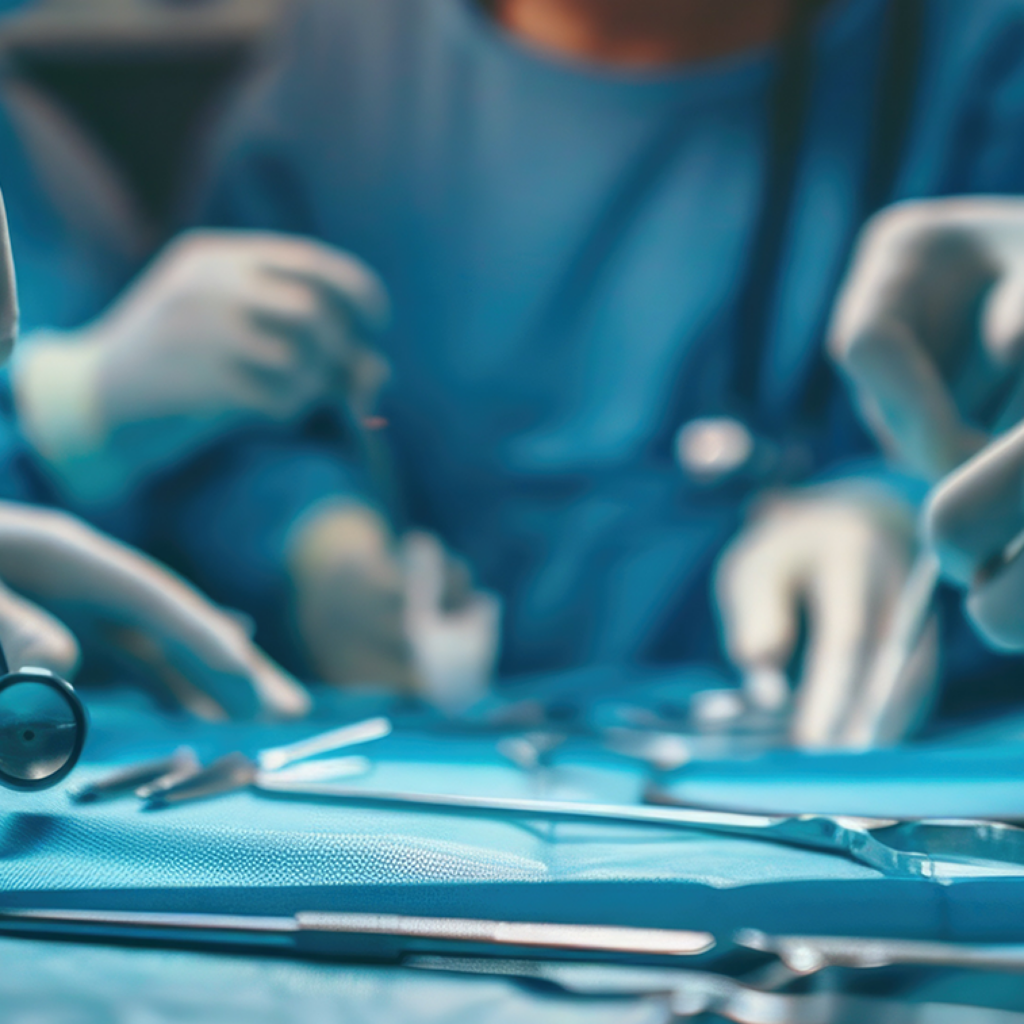
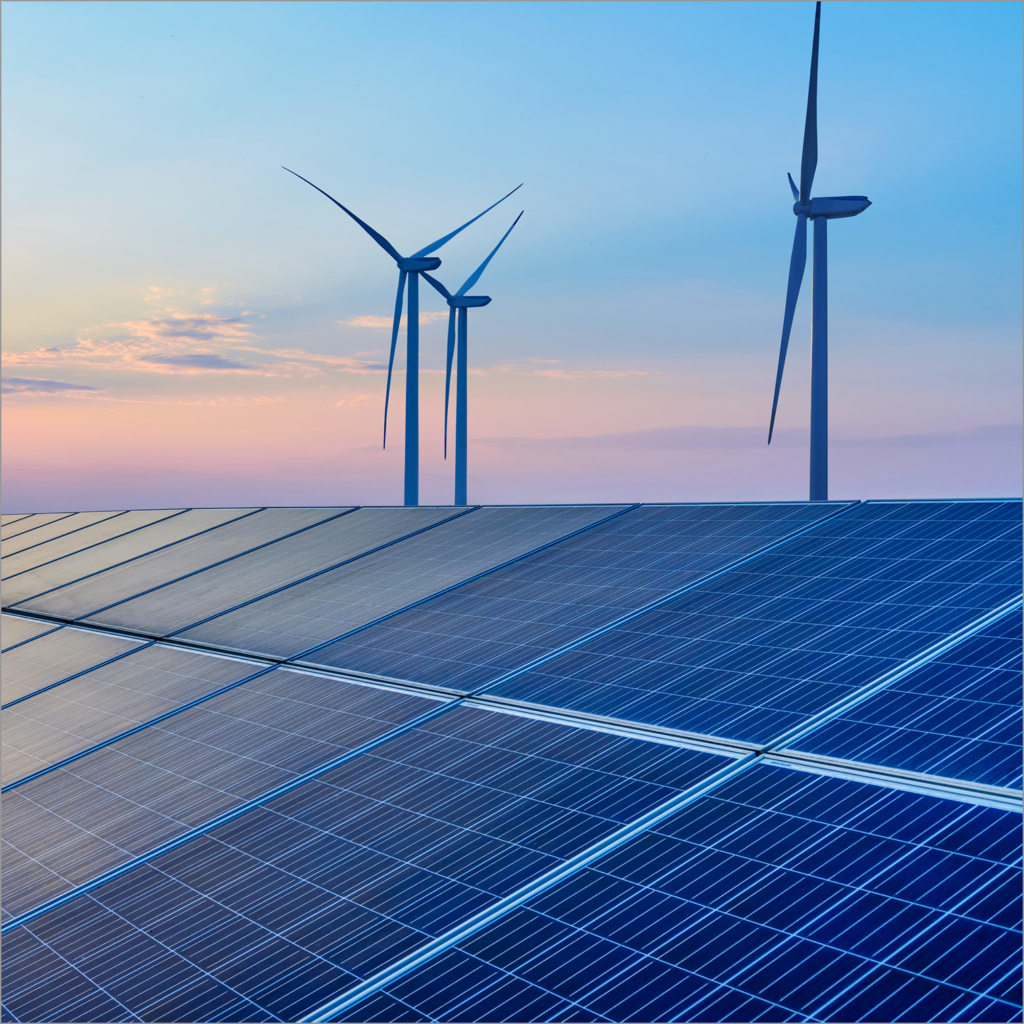
Energy Solutions
From upstream oil & gas to power generation, energy systems demand components that withstand extreme environments and deliver long service life. i3D’s metal 3D printing expertise produces parts—like turbine blades, flow-control valves, and custom manifolds—that meet these challenges head-on.
Corrosion & Temperature Resistance
Print with nickel alloys and stainless steels that preserve strength and integrity in high-temp, corrosive settings.
Complex Internal Channels
Leverage additive freedom to integrate fluid-flow passages and cooling circuits that are impossible to machine conventionally.
Scalable Production Runs
With 30+ machines ready for production, we fulfill both low-volume specialty parts and larger batch requirements without compromise.